认 证:工商信息已核实
访问量:574463
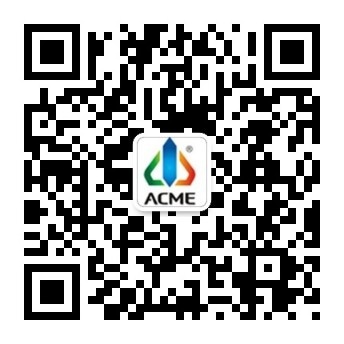
湖南顶立科技有限公司 2018-04-09 点击1706次
面向增材制造球形钛合金粉体制备技术的研究现状与进展
戴 煜1, 2,李 礼1, 2
(1. 湖南顶立科技有限公司,湖南 长沙 410118;
2. 湖南省新型热工装备工程技术研究中心,湖南 长沙 410000)
摘 要:增材制造技术被誉为第三次工业技术革命,制约其发展的核心问题之一仍然是材料。目前,国内大部分金属3D打印粉体材料,特别是钛合金粉体只能依靠进口,价格高昂,而国内钛合金粉体制备技术整体发展较为缓慢,粉末批次稳定性一直未得到解决。为此,本文主要概述了目前国内二流雾化法(无坩埚电极感应熔化气体雾化法EIGA、等离子火炬法PA)、离心雾化法(等离子旋转电极雾化法PREP、电子束旋转盘法EBRD)、球化法(射频等离子球化RFPS、激光球化LS)等几种主流的球形钛合金粉体材料制备技术的基础原理,分析了金属3D打印粉体材料制备技术的现状,制粉工艺及装备的最新进展,评述了各自的优缺点,并指出快速提升国内钛合金粉体制备技术的途径仍将是以上述常见的几种方法为基础进行工艺及设备的改进研究;以机械法(高能球磨法、气流磨粉碎法等)+球化法或物理-化学法(氢化脱氢法、气相法等)+球化法的方式也将开启球形钛合金粉体材料制备新天地。
关键词:增材制造;球形钛合金粉体;二流雾化、离心雾化、球化
随着国家工业的发展,航空、航天、大飞机等现代工业高端领域正在向高参数、极端恶劣条件下高可靠、长寿命服役的方向快速发展,这无疑增加了制造技术的要求与难度。采用传统加工技术对设备的要求愈发苛刻,加工难度也逐渐加大,特别是对钛合金等难加工材料的利用率和加工周期也不尽如人意,因此增材制造技术得到了大力发展的动力与支持。与传统减材制造相比,增材制造采用的是一种全新的制作理念,其特点是:加工速度快,制造形状任意化(无需模具)及制作周期短,材料利用率高;能够实现数字化、智能化、并行化;产品精度较高,具有良好的力学性能,使得增材制造技术在金属成形领域,特别是航空航天钛合金关键部件领域的作用非常突出[1-4]。
2015年,在工业和信息化部、国家发展和改革委员会、财政部3部委的支持下,国内颁布了首份国家级计划—《国家增材制造产业发展推进计划(2015—2016)》(工信部联装【2015】53号),首次将以钛合金为代表的增材制造专用材料纳入其中;同年,李克强总理在全国“两会”中提出“互联网+”行动计划,实施“中国制造2025”等一系列举措,与增材制造“互联网+先进制造技术”独有的行业特点不谋而合,并在国家制造强国建设战略咨询委员会的推动下,颁布了“《中国制造2025》重点领域技术路线图”,其中就明确了发展前沿新材料(低成本钛合金增材制造粉末)的技术路线;2016年,工业和信息化部在大力贯彻《中国制造2025》的基础上,推出《工业强基工程实施指南(2016-2020年)》,继续开展“先进基础工艺”(以钛合金为重点的增材制造工艺)重点方向的工业强基专项行动。毫无疑问,低成本钛合金粉末及其快速增材制造关键共性技术的研究开发,是国家发展的刚需所在。
欲推动我国增材制造技术产业发展,诸多核心问题亟待解决。首当其冲的是材料问题。由于增材制造技术对粉末的性能指标要求很高,沿用现有制粉技术研制的增材制造粉末,从粉末球形度、粉末纯度、粉末均匀性、粉末松装密度、细粉收得率、粉末自给率等方面均难以满足增材制造技术的大规模应用。高端钛合金粉末基本依赖进口,成本高昂(高达4000-5000元/kg),国产钛合金粉末量少质差,难以满足要求是国内增材制造材料的真实写照。随着国内增材制造技术的蓬勃发展,对于球形钛合金粉的需求将呈现几何增长。高纯、低成本、批次稳定的球形钛合金粉制备技术及生产装备已成为国内外竞相开发的重点[5]。
目前,制备球形钛合金粉末主要以二流雾化法、离心雾化法以及球化法为主流制备方法。因此,本文主要概述了上述几种主流的球形钛合金粉体材料制备技术的现状,制粉工艺及装备的最新进展,评述了各自的优缺点,并提出了一些建设性建议。
1 二流雾化法制备球形钛粉
二流雾化法主要是利用高速、高压的流体介质(通常为水或者气体)撞击熔融金属液流,从而引起液流破碎,并在极快的冷却条件下迅速凝固成粉体的过程[6]。二流雾化法具有生产成本低、生产设备及工艺简单、操作安全等优点。
最先开始应用于球形钛粉制备的二流雾化方法为真空气雾化法(VIGA法)。采用VIGA法能够获得不错的细粉率(-300目以下粉末收得率可达70%左右),但粉末球形度一般,同时还存在空心粉、卫星粉、闭孔粉等,最严重的是由于钛合金活性高,VIGA法的水冷铜坩埚材料容易污染钛合金,因此VIGA法不能制造高质量的钛合金粉末。
1.1 无坩埚电极感应熔化气体雾化法(EIGA法)
为消除坩埚的污染,1990年德国开启无坩埚熔化雾化制备钛及钛合金粉末技术,称之为电极感应熔化气体雾化工艺(EIGA法),开辟了一条制备高纯度、高洁净粉末新方法,其原理示意图如图1所示。该技术通过感应线圈将缓慢旋转(5~20r/min)的电极棒(直径16~20mm,长度1500~3000mm)材料熔化并通过控制熔化参数形成细小液流(液流不需要接触水冷坩埚和导流管),当合金液流流经雾化喷嘴时,液流被雾化喷嘴产生的高速脉冲气流击碎并凝固形成微细粉末颗粒[7]。由于不与水冷坩埚和导流管接触,材料不会发生污染,EIGA技术从理论上来说适合制备活性材料粉末,几乎可以制备任何合金材料。EIGA技术优点是能耗较低,其不足之处是雾化效率及细粉收得率上比VIGA法差(-300目细粉收得率不足30%)[8];需要熔炼合金电极,电极的偏析也会导致合金粉体材料的成分不均匀,造成粉末批次稳定性差;同时EIGA法一般采用冷态介质,由于熔体的过热度不够,粉末不具备足够长的冷却时间进行球化,因此粉末球形率很难继续提升,且卫星球比较多。为此,英国某公司与美国某公司联手进行热气体雾化机理的研究,并发现粉末的平均粒度和标准偏差均随温度升高而降低[9]。但是热气体雾化技术受到气体加热系统和喷嘴的限制,目前该项技术仍未实现大规模产业化应用[10-11]。上述这些是该项技术现阶段的短板所在。
图1 无坩埚电极感应熔化气体雾化法结构原理示意图
虽然EIGA存在不足,但是现阶段EIGA法仍是国内大部分企业制备球形钛合金粉体材料的主流方式之一。该方法制备的钛合金粉体材料球形度可达90%以上,粉末松装密度为其致密材料的52%左右,氧含量可控制在500-1400ppm之间。采用EIGA法制备的粉末形貌示意图如图2所示。
图2 无坩埚电极感应熔化气体雾化法制备的钛合金粉末SEM示意图
1.2 等离子火炬雾化法(PA法)
为解决冷态介质引起的球形率不高的问题,美国推出等离子火炬雾化制粉方法(PA法),这种方法具有无坩埚的特点,同时又提高了熔体的过热度,能够生产高质量的金属粉末,是一种非常有前景的方法[12]。加拿大某公司正是采用这种方法制备钛合金粉末。图3是PA法雾化机理的结构示意图。其雾化机理可简要描述为:金属及其合金,或者陶瓷,以一定规格尺寸的棒坯或者原料丝或者不规则/团聚颗粒,或者以液态蒸汽形式,通过特殊的喂料机构(棒料进给系统、送丝机构、线材矫直机、雾化喷嘴等)以恒定速率送入,并在炉体顶部多个等离子火炬产生的聚焦等离子射流下熔融雾化,形成液相。最后通过控制冷却速率,得到球形粉体。
图3 等离子火炬雾化法结构原理示意图
等离子火炬雾化制粉技术可划入二流雾化范畴。与传统的二流雾化工艺相比,该技术摒弃了冷态雾化流体(空气、惰性气体或水)的使用而采用热等离子体作为雾化流体,因此具有足够长的冷却时间保证颗粒充分球化,避免熔融颗粒因快冷形成不规则状;此外,通过将熔融与雾化集中于同一道工序,摒弃了传统陶瓷坩埚的使用,因此该工艺适用于几乎所有具有液相的金属或合金材料的粉体制备,特别像钛合金等这类传统工艺难以制取的高活性材料也可通过本方法获得。与VIGA、EIGA法相比,采用PA法制备的粉末-300目细粉收得率介于VIGA法与EIGA法之间,可达到32%左右;粉末质量整体优于VIGA、EIGA法,具有粒径分布均匀、高纯度、高球形度、流动性好、低氧含量、松装密度高、夹杂少、无粘接/团聚现象等特点,具体如图4所示。
图4 等离子火炬雾化法制备的钛合金粉末SEM示意图
目前,国内有两家企业采用了从加拿大引进的PA法雾化技术与装备。湖南顶立科技有限公司通过引进消化再吸收,开始着手新一代等离子火炬雾化制粉技术及装备的研制,该项目拟从多角度大功率(150KW)等离子火炬雾化技术、精细化细丝(0.2mm~0.25cm)喂料技术、特种高速喷嘴结构设计技术、粉体收集与分离技术等关键技术进行科技攻关,以期研制出具有自主知识产权的新一代等离子火炬雾化制粉技术及装备。预期通过该装备制备的粉末球形率可达到95%以上,粉末松装密度可达到其致密材料的58%以上,粉末氧含量可控制在原丝氧含量水平(低于1000ppm),细粉收得率也可达到42%以上。
2 离心雾化法制备球形钛粉
离心雾化法是将熔融金属液流从坩埚或浇注包浇注至旋转的圆盘或杯中,或者直接熔化高速旋转的金属棒料的一端,使金属液流在旋转离心力的作用下破碎成小液滴,随后快速凝固形成金属粉末。离心雾化法制备的粉末基本为球形、实心、较致密、粒度分布较窄、流动性能好及松装密度高,粉末粒径可通过旋转载体的转速与直径来控制,但是采用该法细粉收得率极低。以离心雾化法制备的钛合金粉体材料为原料,可制得机械性能好、致密化程度高的部件,但是其成本较高,一般推荐用于要求极高的航空航天、生物医疗等领域[13-14]。
2.1 等离子旋转电极雾化法(PREP法)
等离子旋转电极雾化法(PREP法)最先是用于粉末高温合金、钛合金的最主要的方式之一。图5是PREP法雾化制粉的原理结构示意图。其基本原理可表述为:将金属或合金制成自耗电极,自耗电极端部在同轴等离子体电弧加热源的作用下熔化形成液膜,液膜在旋转离心力的作用下被高速甩出形成液滴,熔融液滴与雾化室内Ar气摩擦,在切应力作用下进一步破碎,随后熔滴在表面张力的作用下快速冷却凝固成球形粉末[15]。PREP法粉末的最大优势是粉末表面清洁、球形度高、夹杂少、无空心粉。但是传统的PREP法由于电极棒的直径小(≤50mm)、转速低(极限转速15000r/min),制备的粉末粒度比较粗大,-300目细粉收得率较低。新热源技术应用(激光、电子束、等离子火炬)、提高电极棒直径与极限转速、攻克高速动密封技术是PREP法技术关键[16-20]。
图5 等离子旋转电极雾化法结构原理示意图
国内等离子旋转雾化制粉技术的研究大体可分为两类。一类是以直接引进俄罗斯最先进的制粉技术及装备为基础,开展金属3D打印粉体的研制工作,如国内某些科研院所,采用的是俄罗斯V公司第二代等离子旋转雾化制粉技术及装备。另一类以西北地区某些制粉企业为代表,以俄罗斯七十年代的技术及装备为基础,通过引进-消化吸收-再创新的方式进行自主研发,制备技术方面主要包括电极棒转速及直径、等离子弧电流强度、等离子枪与电极棒端部间距、电极棒进给速度等工艺参数研究;设备方面主要包括旋转电极制粉设备改造、旋转电极制粉机组的设计开发、旋转电极制粉设备的报警系统研制、高压等离子点火装置以及等离子枪的改进等。取得了一些成绩,但是总体上来说,国内研发成果相对较少、改进力度不大、质量不高,与国外相比差距还较大,细粉收得率(-300目以下)不到5%。湖南顶立科技有限公司通过自主研发,已经完成第二代、第三代、第四代等离子旋转雾化制粉系统的研制工作,新一代等离子旋转雾化制粉系统(四代机)整机性能可与俄罗斯最新的技术比肩,棒料直径提升至80~100mm,棒料极限转速达到22000~30000r/min,细粉收得率可达16%左右。为满足国内科研院所的快速、小规模新型粉体材料研究需求,顶立科技近期正在研制一种“桌面级”等离子旋转雾化设备,该设备尺寸小(Φ700×200mm),棒料直径20-30mm,棒料极限转速高达50000-60000r/min,产能可达到20-30kg/天(以TC4计),-300目细粉收得率高达40%以上。
相对于气雾化技术,PREP工艺不以高速惰性气流直接分散金属液流雾化,因此可以避免气体雾化法中出现的“伞效应”,因此等离子旋转电极法制备粉末粒度分布更集中;采用气雾化,高速Ar气流对熔体的冲击分散易在粉末颗粒内部形成闭合孔隙,该闭孔内含有一定量的Ar气体,而采用等离子旋转电极雾化法制得的粉末球形度更高(>99%)、氧含量低(50~500ppm)松装密度高(58~60%)、流动性更好、气体体积分数低,是金属3D打印的理想原料,PREP制备的金属粉末SEM形貌如图6所示;此外,等离子旋转电极雾化制粉技术能有效杜绝陶瓷夹杂物。
图6 等离子旋转电极雾化法制备的钛合金粉末SEM示意图
2.2 圆盘旋转雾化法(CA法)
图7是圆盘旋转雾化法的结构原理示意图。圆盘旋转雾化法是将熔化的金属液流连续滴落到一个高速旋转的碟盘上(转速高达35000r/min以上),然后经离心力作用分散细化形成液滴并沿着碟盘边缘甩出,甩出后受到高速氦气流的强制对流冷却,液滴快速凝固形成球形粉末[21-22]。碟盘的形状可以是圆盘状、杯状或简易的平板状、雾化室的惰性气体通常采用氦气,而不用氩气,以增加冷却速率,减小设备雾化室尺寸。
图7 圆盘旋转雾化法结构原理示意图
CA钛合金粉末中会包含一些闭孔,闭孔内通常含有部分雾化气体如氦气,在后续3D打印过程中不易排除,易发生热诱导空隙长大。德国某研究中心分别对CA法、EIGA法、VIGA法3种制粉技术进行了粉末中闭孔夹杂的气体含量对比研究[22]。结果表明,CA法技术制备的粉末闭孔内夹杂气体最多、EIGA法次之、VIGA法最低。利用氦气代替氩气也不能解决闭孔中夹杂惰性气体的弊端。此外,CA法容易引起的问题有坩埚漏嘴的污染和旋转圆盘的变形,尤其在生产钛合金等活性粉末时问题更加突出。因此,该项技术国内鲜有企业使用。采用CA法制备的粉末形貌如图8所示。
图8 圆盘旋转雾化法结构原理示意图
为避免坩埚污染,德国某公司[23]发明了一种电子束旋转圆盘雾化法(EBRD),其原理是以电子束为热源(可以3个电子束同时工作),熔炼缓慢旋转(10~50r/min)的合金棒料,并加热快速旋转的水冷圆盘(4000~15000r/min),合金棒料形成的液流经高速水冷圆盘甩出破碎成小液滴,快速凝固形成球形粉末。EBRD法原理结构示意图如图9所示,该方法存在的弊端是:在反射屏上易形成二次雾化;熔点低于1800℃的金属生成片状粉末;粉末易粘在反射屏上;真空环境下,低熔点金属易挥发等。
图9 电子束旋转圆盘雾化法结构原理示意图
3 球化法制备球形钛粉
球化是利用温度高、能量密度大的热源,将形状不规则的钛合金原料粉体迅速加热而熔化或气化,然后在极高的温度梯度下迅速冷却固化或沉积,最终得到球形钛合金粉体颗粒的过程[24-25]。目前,球化法制备球形金属粉末主要有射频等离子球化法(RFPS法)和激光球化法(LS法),以及其他热源的球化。如前面叙述的PA法,如等离子火炬功率足够大,取消雾化喷嘴,直接气化金属原料,从某种意义上也可归结为球化法。
3.1 射频等离子球化法(RFPS法)
射频等离子球化法是利用射频电磁场的感应作用对各种气体进行感应加热,产生射频等离子,利用高温的等离子体熔化非球形粉末,熔融的粉末颗粒在自身表面张力以及极高的温度梯度的共同作用下,迅速冷凝形成球形度很高的小液滴,从而获得球形粉末[26-27]。其装置原理结构示意图见图10。射频等离子球化技术被公认是获得致密、规则球形颗粒的最有效手段之一[28]。
图10 射频等离子球化法结构原理示意图
国际上加拿大在射频等离子球化技术领域处于领先位置,已经实现钛、钨、钼、钽等金属粉末的球化处理[29]。国内,某些科研院所也成功研制出射频等离子球化技术及装备,并成功以TiH2作为原料,采用射频等离子球化技术制备出球形度高(球形率>85%)、表面光洁、粒径细(20~50μm)的球形钛粉[30-31]。射频等离子体球化法的优点如下:可提高粉末球形度,较好地改善粉末流动性;可消除颗粒内部的孔隙,提高粉末松散度;可适当改变颗粒表面形貌,提高粉末纯度。但是由于射频等离子球化过程中会出现熔融碰撞、汽化再结晶等因素,会导致一定数量的大颗粒形成,因此被球化的非球形粉末颗粒不能过大[32]。图11是经射频等离子球化前后粉末形貌对比图。
图11 经射频等离子球化后粉末形貌对比图
(a) 球化前; (b)球化后
3.2 激光球化法(LS法)
金属粉末在激光选区烧结(SLS)过程中发生球化效应是一个常见的现象,即当激光束扫过粉末表面时,粉末迅速升温熔化,之后再表面张力作用下收缩成球形颗粒,激光选区烧结产生的球化现象如图12所示。因此,利用激光球化法(LS法)可将普通不规则钛合金粉末制备成球形粉末。
图12 激光选区烧结过程中发生的球化效应
湖南某高校[33]通过改变激光功率与扫描速度,以氢化脱氢法制备的异形钛粉为原料,成功获得了较为理想的球形钛粉,粒度分布范围为10~250μm。试验结果表明,采用LS球化技术进行球化是获取球形粉末的一种可行途径。此外,还有以氢氧焰燃烧等多种热源进行异形粉末球化的球化方式,并成功制备出平均粒径在150μm左右的球形钛合金粉体,如湖南顶立科技有限公司自主研制的高温球化设备,在3000℃以上的高温下球化获得球形钛合金粉末。笔者认为,以机械法(高能球磨法、气流磨粉碎法等)[34]+球化法或物理-化学法[35-36](氢化脱氢法、气相法等)+球化法或水雾化、气雾化+球化法的方式也将开启球形钛合金粉体材料制备新天地。
4 球化钛合金粉制备技术比较
综上所述,二流雾化法、离心雾化法、球化法三类制备方式有着各自优缺点:
①真空气雾化制备的钛合金粉末细粉收得率较高,球形度较好,成分较易控制,但明显存在卫星颗粒及空心粉末,另外无可避免引入陶瓷夹杂;
②无坩埚电极感应熔化气体雾化法、等离子火炬雾化法是制备球形钛合金粉体材料的理想方法之一,但是仍无法完全解决卫星颗粒及空心粉末的问题,且现阶段细粉收得率不是特别理想;
③离心雾化法制备的粉末球形度高,粉末实心,无卫星颗粒及空心粉末,成分易于控制,是制备球形钛合金粉体材料的理想方法之一,但是粉末颗粒的细化依赖于旋转速度,细粉收得率极低;
④球化法制备的粉末流动性好,松散度高,粉末颗粒内部的孔隙与裂缝明显减少,粉末纯度高,表面形貌好,该方法与传统机械法或物理-化学法组合将是一种前景较好的球形钛合金粉体材料的制备方法,但受限于工艺连续性及设备,整体上劣于二流雾化与离心雾化。
表1 国内金属3D打印粉体材料制备方法对比
工艺方法 | 简称 | 成本 | 球形率(%) | 细粉收得率 (-300目) | 松装 密度 (%) | 流动性 | 氧含量 (ppm) | 可制取粉末 | |
二流雾化法 | 无坩埚电极感应熔化气体雾化法 | EIGA | 高 | 90 | <30% | 52 | 中 | 500-1400 | 任何金属 |
等离子火炬雾化法 | PA | 较高 | 95 | 32% | 58 | 较好 | <1000 | 任何金属,包括陶瓷 | |
离心雾化法 | 等离子旋转电极雾化法 | PREP | 较高 | 99 | 15% | 60 | 好 | 50-500 | 任何金属 |
圆盘旋转雾化法 | CA | 高 | 95 | 10-15% | 52-55 | 较好 | <1000 | 任何金属 | |
球化法 | 射频等离子球化法 | RFPS | 中 | 85 | 50% | - | 较好 | 1000-2000 | 高熔点金属 |
激光球化法 | LS | 高 | 95 | 20% | 58 | 好 | 500-1400 | 低熔点金属 |
5 结 语
随着金属3D打印产业的发展,球形钛合金粉体材料的制备技术将进一步完善及产业化,老一代技术将得到大幅度更新换代,新的制备技术及工艺也将不断涌现。目前,国内钛合金制粉技术整体水平仍停留在中试阶段,其工艺稳定性有待进一步提高,离实现工业化批量生产还有一段距离。为了提高国内钛合金粉体材料制备技术的适用性,最快的途径仍将是以上述常见的几种方法为基础进行工艺及设备的改进研究。随着金属3D打印的热潮继续,预计EIGA法、PA法、PREP法制备球形钛合金粉体材料的技术及装备将得到更进一步的发展。此外,以机械法(高能球磨法、气流磨粉碎法等)+球化法或物理-化学法(氢化脱氢法、气相法等)+球化法的方式也将开启球形钛合金粉体材料制备新天地。